ScanBox Series 5
Flexible and expandable measuring system for complex components
With its modular concept, the ZEISS ScanBox Series 5 redefines the flexibility of automated inspection and digitization of complex components. With its three individually customizable models, it enables tailor-made solutions for a wide range of requirements.
The series not only offers the option of scaling to larger component sizes, but also supports the precise measurement of add-on parts, assemblies and airfoils with optional layout upgrades.
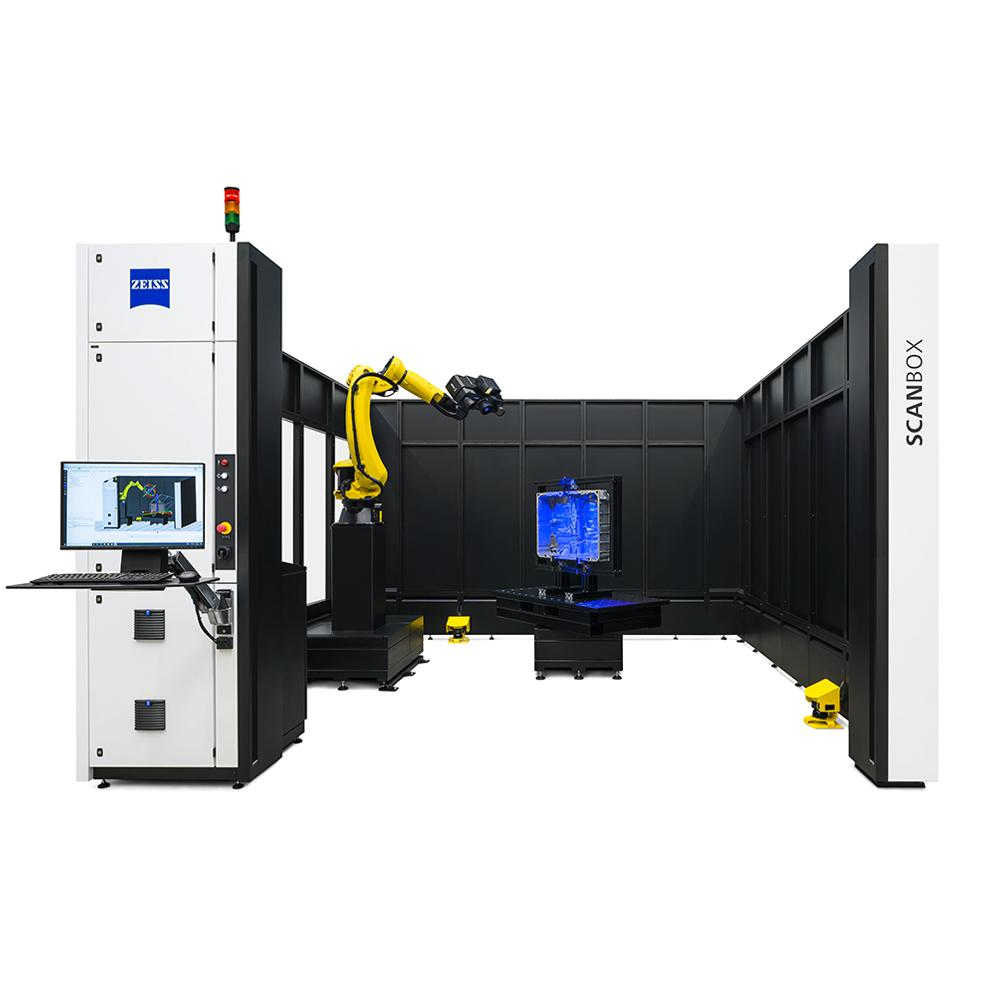
- Automated quality control
- Worker service
- For medium to large components
- Modular and flexible
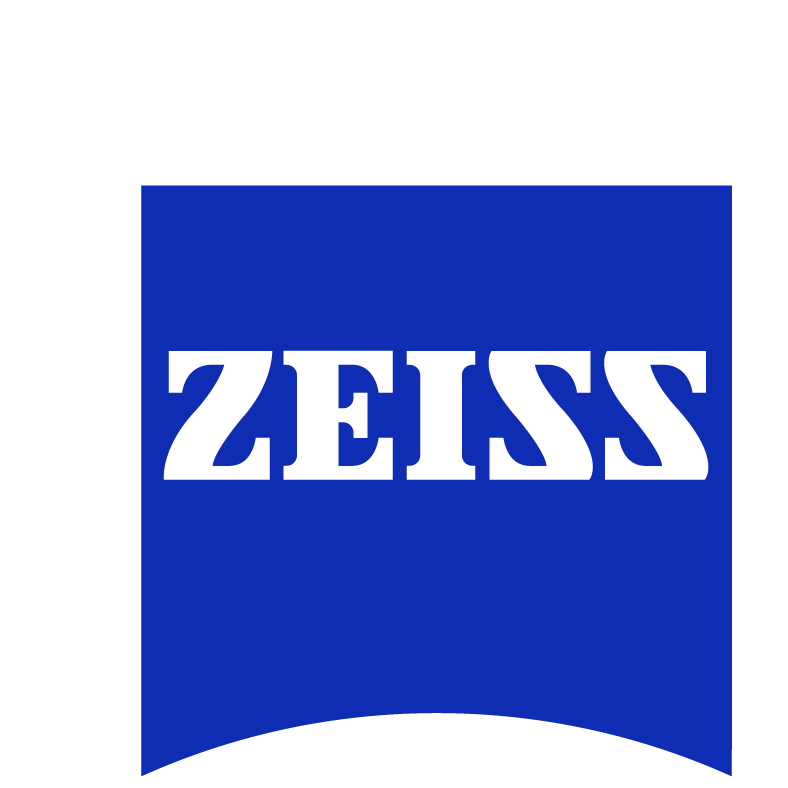
Automated production control
The optical 3D measuring machine provides you with full-surface measurement results for CAD comparison in the shortest possible time, visualizes possible form and position deviations and speeds up your production, maintenance and repair processes. Use the system to quickly capture specific measurement features and geometries, such as surface and edge points, holes or bores.
Standardized and automated processes increase the throughput of components and reduce rejects. The ZEISS ScanBox Series 5 systems enable a high level of process reliability during operation thanks to real-time trend analyses.
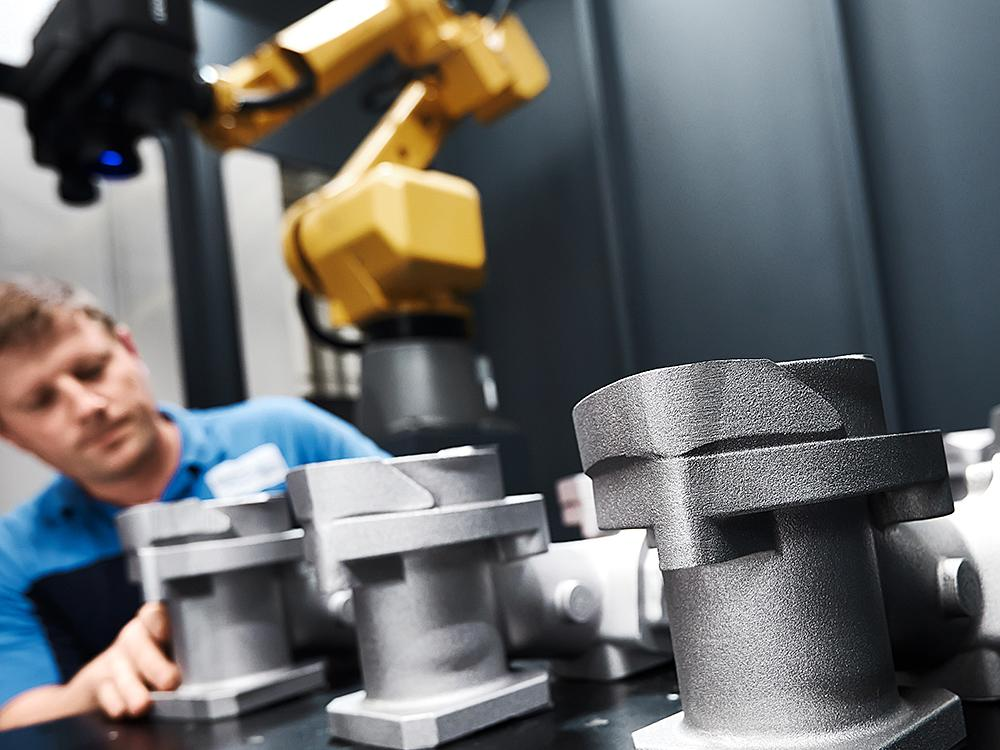
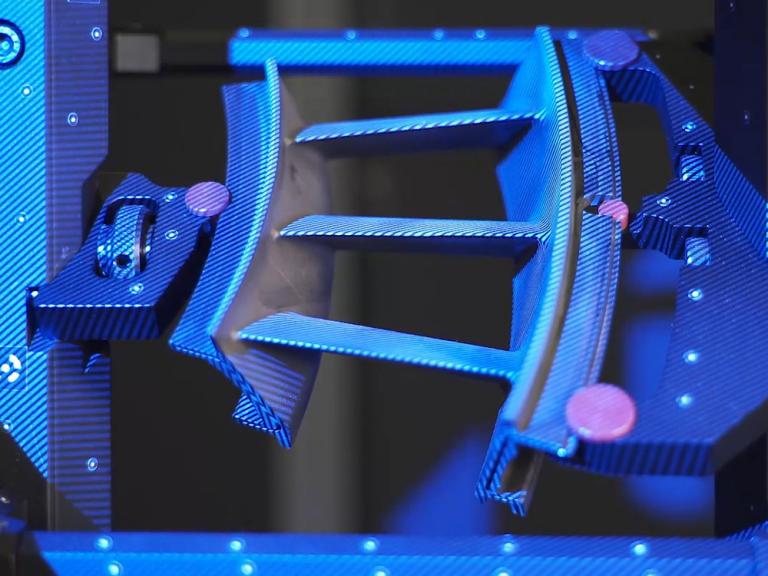
Tailor-made for airfoil inspections
The ZEISS ScanBox 5110 is particularly suitable for the inspection of turbine blades. Specially developed for the gas turbine industry, ATOS 5 for Airfoil delivers high-precision 3D data of the smallest details with an optimized working distance and measuring fields from 100 x 70 mm².
You can measure a complete blisk in less than an hour. It only takes a few minutes to inspect a turbine blade.
Ergonomic operation
You can operate the ZEISS ScanBox while standing or sitting. The flexible user interface offers various ergonomic functions. A swivel arm integrated in the electronics cabinet can be adjusted to the desired position so that the ZEISS ScanBox Series 5 can be operated while standing or sitting.
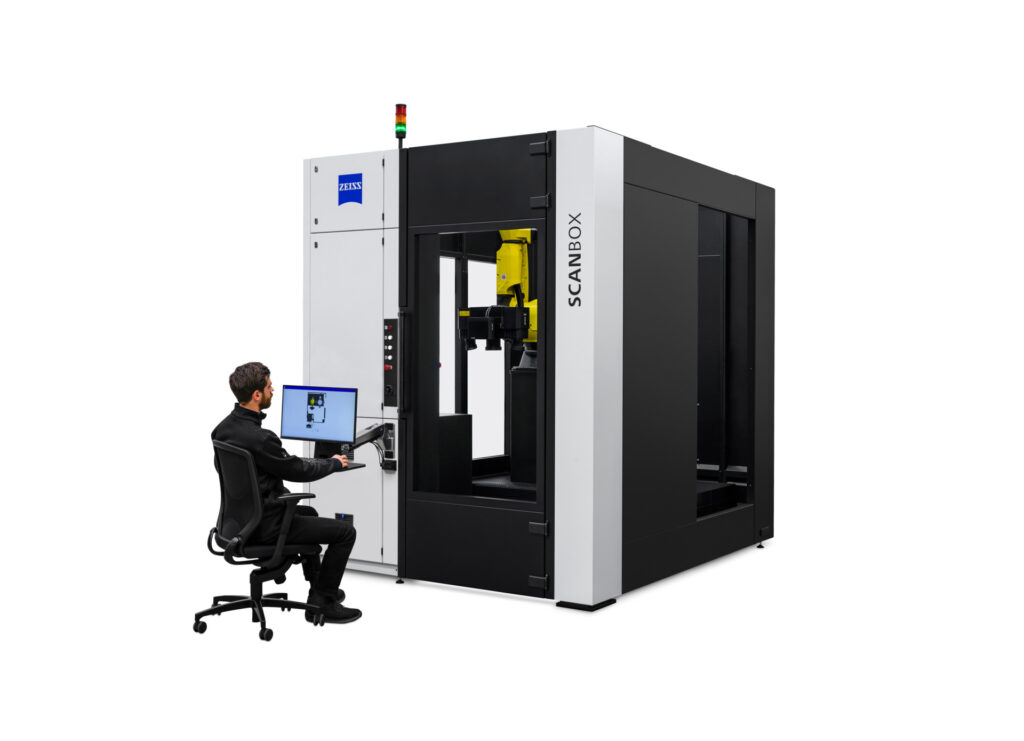
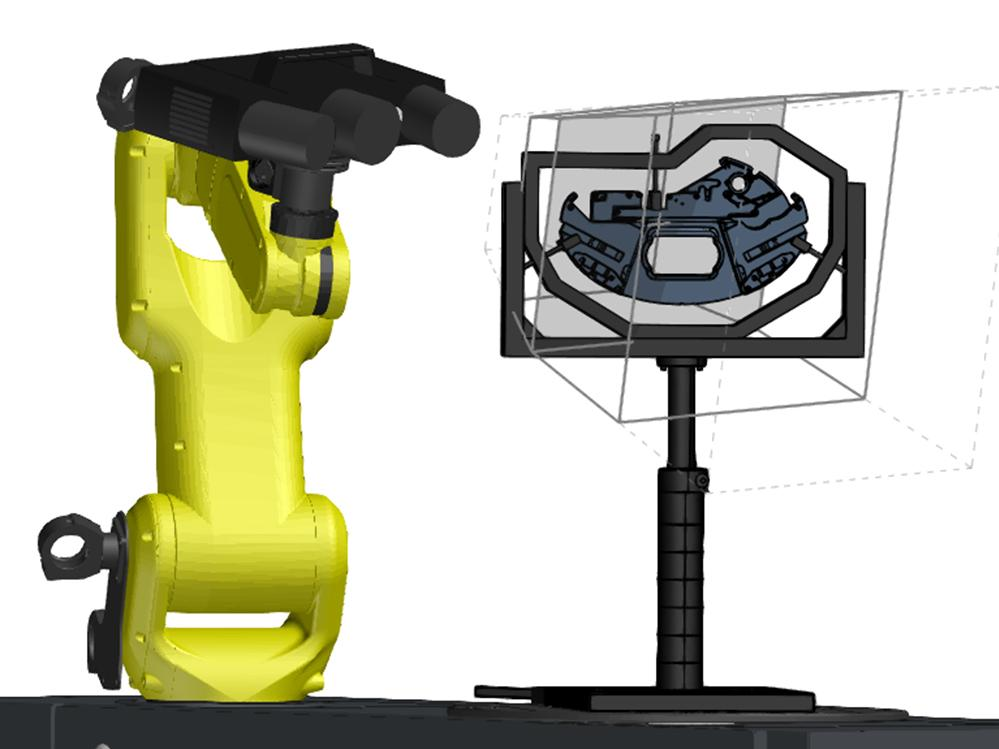
Virual Measuring Room
The virtual measuring room (VMR) is the central control and planning tool for ZEISS ScanBox. Here, the real environment is depicted in a precise virtual simulation.
The VMR includes a robot with sensor, enables the programming of the robot paths and the creation and execution of the measurement plan. Thanks to the VMR, no special robot knowledge is required: all movements are simulated in advance and checked for safety before execution.
Analysis tool included
WESTCAM offers everything from a single source: scanning, checking and reporting for detailed target/actual comparisons as well as shape and position tolerances. The easy-to-understand results enable you to implement any necessary corrections directly.
Carry out comprehensive analyses, create detailed reports and integrate the measurement results seamlessly into your existing processes.
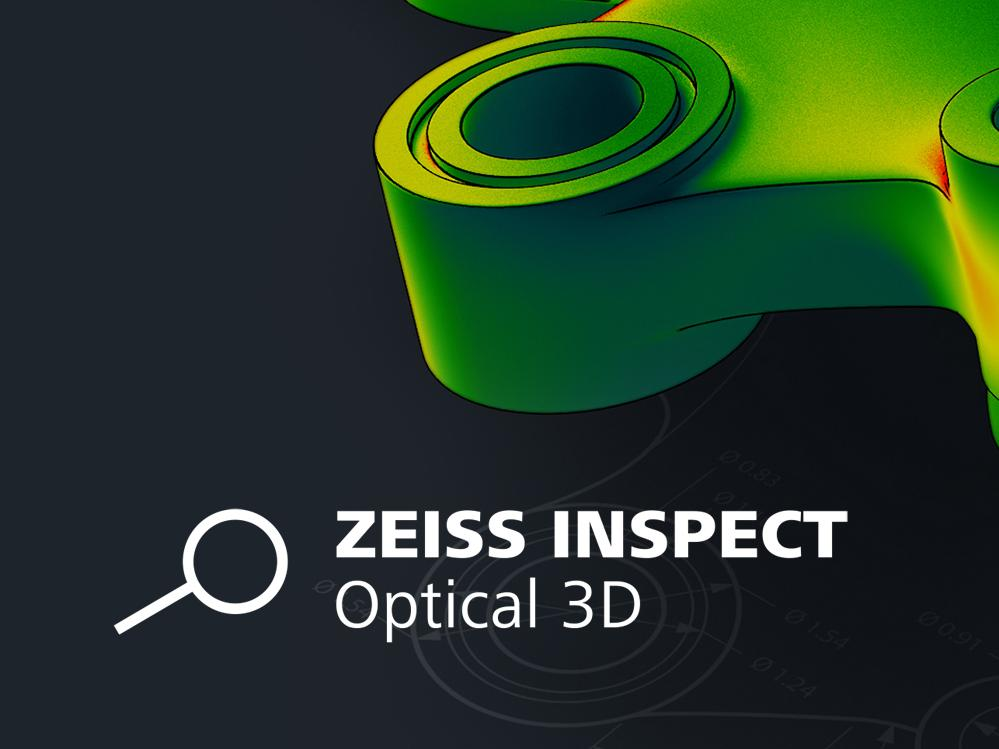
ZEISS ATOS ScanBox – Virtual Clamping Technology
Customer reference BENTELER automotive supplier
Frequently asked questions (FAQs)
Welche Vorteile bietet die ZEISS ScanBox Serie 5 für die automatisierte Bauteilprüfung?
The ZEISS ScanBox Series 5 offers a modular concept for the precise inspection and digitization of complex components. With three customizable models, it enables flexible solutions and optional upgrades to different layouts, ideal for add-on parts, assemblies and airfoils.
Wie unterscheidet sich die ZEISS ScanBox Serie 5 zum Vorgängermodell?
Compared to its predecessors, the ZEISS ScanBox Series 5 is characterized by an extended modular measuring system that supports component sizes up to 3000 mm. Thanks to identical components, upgrades to larger layouts are possible at any time, which offers optimized adaptability.
Welche Rolle spielt die ZEISS ScanBox Serie 5 in der industriellen Qualitätssicherung und Prozessoptimierung?
The ZEISS ScanBox Series 5 is a decisive tool for industrial quality assurance and process optimization during series production. It can be easily operated in series production by semi-skilled workers – trained application personnel are only required for the initial program template creation. Measurement results are stored centrally and used for process optimization.
We advise you personally!
Gladly there for you
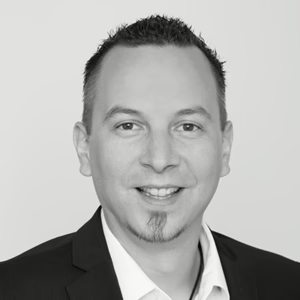