hyperMILL Probing
Workpiece measurement and probing
Take your CNC production to a new level with hyperMILL3D measuring. Our advanced software solution enables precise workpiece measurement and zero point determination directly on the machine tool.
This optimizes your process automation and significantly improves quality control.
Smooth cooperation between CAM programmers and machine operators is crucial to ensure reliable production. Manual interventions and the resulting machine downtimes are often underestimated time wasters that unnecessarily increase production time. With the integrated measurement functions of hyperMILLPROBING, these problems can be solved efficiently and automatically.
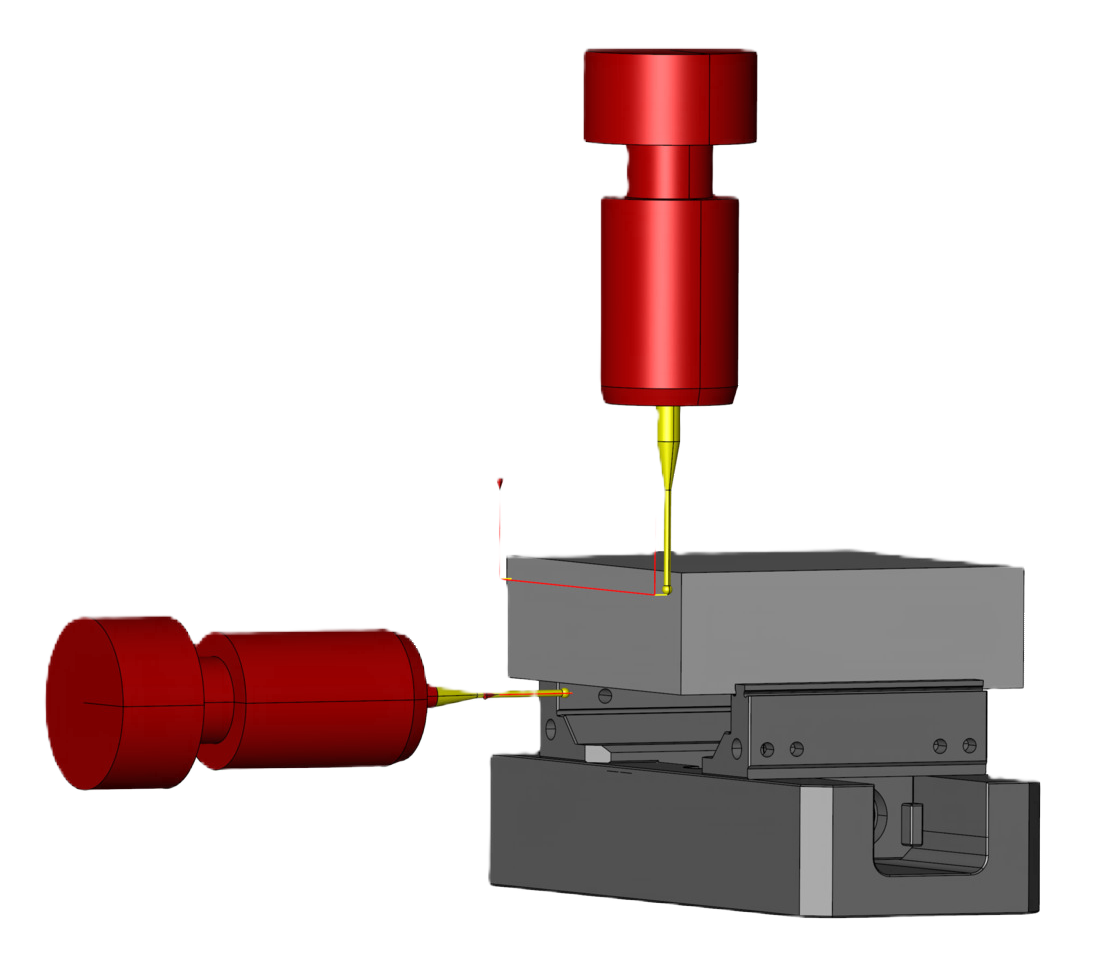
- Process-integrated workpiece measurement and zero point determination
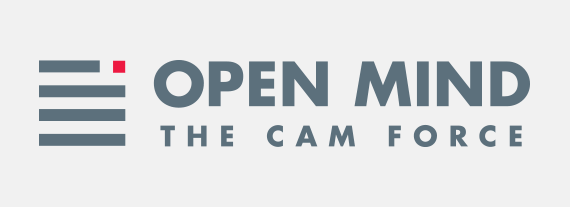
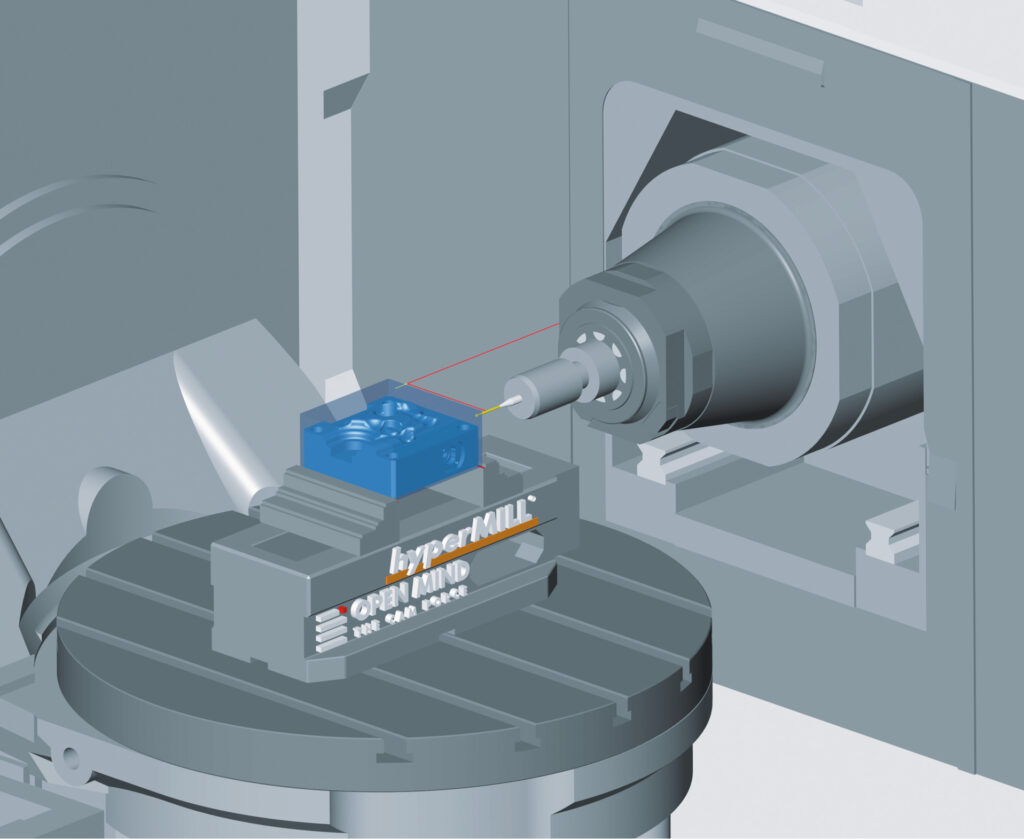
Process-integrated workpiece measurement and zero point determination
The integrated workpiece measurement and zero point determination are decisive advantages of hyperMILL 3D measuring. You can verify blanks and fixtures before machining begins and ensure that the workpiece is optimally positioned.
By probing raw parts and checking the fixtures, you reduce sources of error and increase the precision of your production. You can also measure grooves, for example, and have hyperMILL automatically adjust the machining process to ensure that the result is within tolerance.
After milling, quality control is carried out directly in the original set-up. The use of touch probes makes it possible to reliably measure many features directly on the machine tool, which shortens throughput times.
The measurement results are automatically saved in the machine control system and can be output as measurement reports. These measuring points can be read back in hyperMILL to immediately detect and compensate for deviations. This saves time and improves quality – a function that can also be used on the hyperMILL SHOP Viewer.
hyperMILL3D measurement offers a wide range of measurement strategies, including:
Workpiece alignment via edge or holes: Optimum alignment and zero point determination. |
Rectangular and circular element measurement: Precise measurement of geometric elements. |
Groove and web measurement: Detailed inspection of grooves and webs. |
Axis-dependent measurement: Adjustment and compensation of deviations. |
3D point measurement: High-precision measurement of free-form surfaces, even on 5-axis machines. |
Your advantages with hyperMILL 3D measuring
Reduces manual intervention and increases efficiency.
Integrated measuring processes shorten processing times.
Maximum accuracy in workpiece measurement and quality control.
Simple creation and retrieval of measurement data and logs.
Frequently asked questions (FAQs)
Welche Vorteile bietet hyperMILL 3D Messen?
hyperMILL 3D measuring enables precise workpiece measurement, reduced throughput times and improved process reliability thanks to process-integrated measurements.