Making a vice is a true classic in the metal industry. Almost every apprentice or student has already made a vice as part of a training course. But can such a traditional test piece also be produced using modern processes such as 3D printing?
The challenge
A functioning clamping device in just 8 hours
We wanted to know exactly: Is it possible to produce a fully functional, customized and precise vice within one working day?
Without compromising on functionality? Additive manufacturing provides the answer!
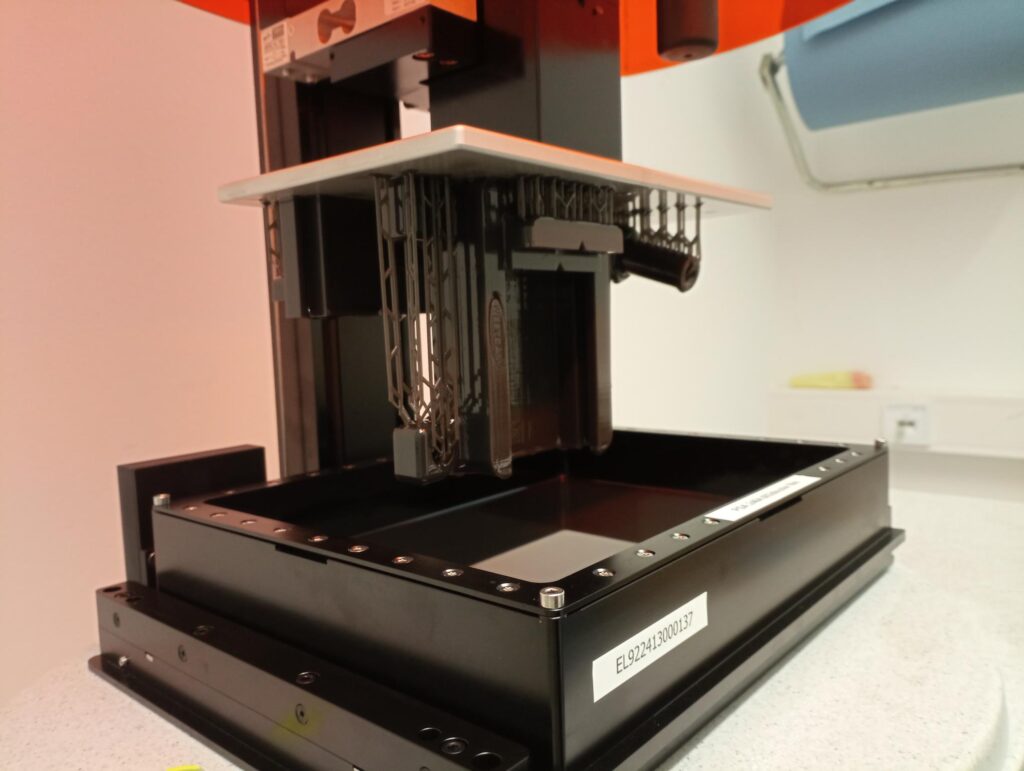
More flexibility thanks to 3D-printed vice jaws
Standard metal vices are robust and proven clamping devices. However, there are applications where individual adaptations are required. This is precisely where 3D printing shows its strengths:
With additive manufacturing, individually designed jaws can be created within a few hours that are perfectly tailored to specific workpieces. Printing functional surfaces, such as threads and guides, promotes accuracy and precision that cannot be taken for granted.
This technology not only enables optimum fixing, but also gentle processing of sensitive materials. Particularly in jewelry manufacturing, electrical engineering or Metrology, 3D-printed clamping fixtures offer completely new possibilities for precise and delicate work.
Hard facts about the DLP 3D printing process:
- Speed: Vices can be produced within one day using DLP technology.
- Precision: The finest details and high-precision jaws and guides are possible.
- Flexibility: The component size is individually scalable and customizable.
Conclusion: Revolution in clamping technology
Additive manufacturing allows faster, more precise and more flexible production of clamping devices than ever before. 3D printing is a real innovation for customized clamping solutions and shows that proven test pieces can be taken to a new level with modern technology!