In comparison: traditional vs. additive manufacturing
Traditional or subtractive methods are still the number one manufacturing process in the industry. However, additive manufacturing is still on the rise thanks to 3D printing technology. What distinguishes the two manufacturing methods? What are the ideal areas of application? And what role will the two technologies play in series production in the future?
There & away: Additive & subtractive processes
Whether at home, in art or in industry, there are two basic methods available to anyone who wants to create something. The first is addition. The end product is created by adding (e.g. layering materials on top of each other, assembling something). Secondly, new things can also be created by taking something away or subtracting something from the initial product. This process is known as subtraction. The most suitable method is selected depending on the area of application. It is the same in industry. In order to understand when which method is preferable, let’s first take a closer look at the two production methods.
Traditional: subtractive manufacturing
Subtractive manufacturing is a traditional method in industrial production. The starting materials are rectangular or round metal and plastic blocks, which are removed in a targeted manner until the desired shape is achieved. During the process, the material is removed by turning, milling, grinding and drilling. CNC machining is based on CAD data from a 3D model designed on the computer.
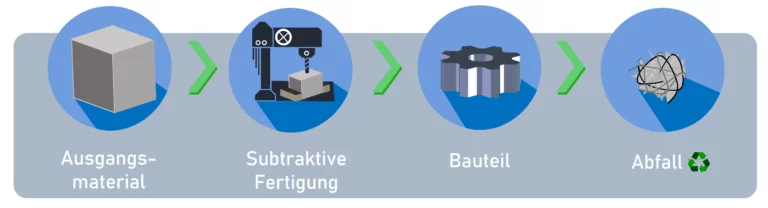
Modern: additive manufacturing
In additive manufacturing, on the other hand, the basic principle is that material is applied layer by layer to create the desired component piece by piece. In this case too, 3D data forms the basis. The 3D printer then produces the component. The printing process differs depending on the technology. The starting material is currently either a plastic strand, a liquid polymer or plastic or metal powder.
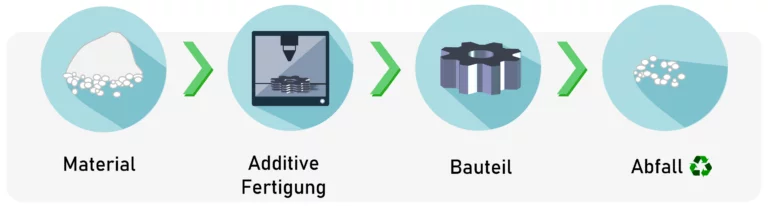
Advantages and disadvantages of the procedures
Advantages of subtractive manufacturing
- Processing of all solid materials regardless of melting point
- Significantly more isotropic material properties
- Realization of different surface finishes (from smooth to rough)
Advantages of additive manufacturing
- Function-oriented design: production of complex shapes possible and therefore great freedom in the design process
- Enormous time savings compared to traditional methods, as production can begin immediately after creating the 3D model
- Cost-effective production, especially for small quantities
- Little waste
- Ideal for prototypes thanks to time and cost savings compared to traditional methods
- Design changes do not require time-consuming adjustments to the production process
Disadvantages of subtractive manufacturing
- Long preparation time until the start of production
- High fixed costs for preparation and manual activities
- Comparatively high production waste
- Machining generally leads to high unit costs
- Very slow with design changes
- Production-oriented design: The design must adapt to the production technology used, but not to the desired function
Disadvantages of additive manufacturing
- Relatively high costs when processing metal, cost savings currently only for materials with a lower melting point (plastics)
- Mostly rough surfaces (due to the layered structure), these must be refined in post-processing
- The final component may have anisotropic material properties (depending on the technology)
Practical check: Which process for which product?
As already described, subtractive manufacturing is the conventional process for component production. This is mainly due to the fact that components must comply with tight tolerances, which is why precision is particularly important. Subtractive processes are also always used when simple geometries need to be implemented. Additive processes, on the other hand, are unbeatable when something needs to be produced particularly quickly and cost-effectively – as is the case with prototypes, for example. Additive processes are also preferable for series with small quantities and complex components.
The two different approaches can also be combined with each other. For example, components are first created using 3D printing and then machined using appropriate tools.
Quo vadis, series production?
Where is industrial series production heading now? Both processes have developed steadily over the years. However, the additive process in particular is currently revolutionizing plastics series production. On the one hand, in the area of product innovation. Complex geometries that are optimized for the performance of the products are just as easily possible as the individualization of components.
On the other hand, progress is also evident in the area of process innovation:
- Time to market: lead times are shortened and the introduction of new products is accelerated.
- Volume: Thanks to advancing development, tens of thousands of units can now be produced in series, and in just a few years there will be hundreds of thousands.
- Inventory: Lower storage costs, as no minimum quantities need to be produced due to the elimination of tool costs.
- Costs: Time-consuming and labor-intensive processes such as machining are eliminated.
- Supply chain: Entire assemblies are combined into one component. This minimizes dependency on multiple suppliers.
- Transport routes: Data can be transferred digitally worldwide and produced directly at the place of use on a 3D printer. This minimizes the CO2 footprint of products.
Conclusion
Both subtractive and additive manufacturing methods have influenced and even revolutionized the manufacture of products. Developments over the next few years will show where the journey will take us. Ultimately, each component or product requires an individual decision as to which method is the best in terms of quantity, costs and requirements. For components with complex geometries, it should also be noted that subtractive manufacturing processes reach their limits much more quickly here.