3D printing | Challenge accepted. “Innovation firmly under control”- 3D printed tractor joystick. Classic injection molding? Or innovative 3D printing? Lindner Traktoren relies on joysticks from the 3D printer
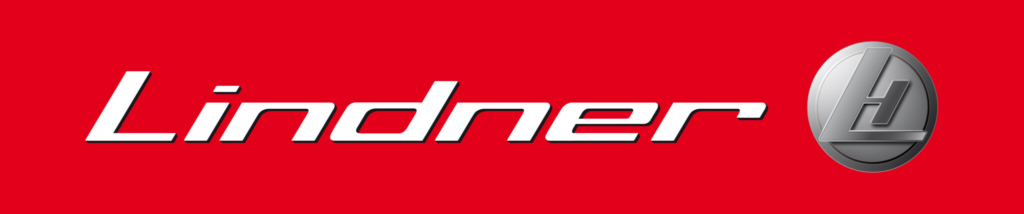
The challenge
The renowned Austrian tractor factory LINDNER with its headquarters in Kundl/Tyrol was faced with a decision:
Continue to manufacture the control levers/joysticks for the driver’s cabs using injection molding or break new ground?
Previously, the joysticks were manufactured in 2 parts using the injection molding process. This required two injection molds and caused additional assembly work.
Every Lindner tractor has a joystick that can be used to control a wide range of functions. But not every tractor has the same one. Because individual customer wishes come first. How can small series be produced quickly, to the highest quality and at low cost?
The time was ripe to think about alternatives. It wouldn’t be LINDNER if we didn’t want to be one step ahead here too. No sooner said than done!
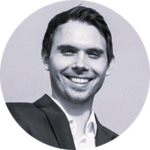
Due to individual requests from our customers and the requirements for special small series, we had to look for alternatives to injection molding production. WESTCAM provided us with competent support and took over the production of the joysticks for us
The solution
Plastic 3D printing: After thorough testing, a critical comparison of processes and precise calculations at LINDNER, it was clear that we would rely on 3D printing in the future! Instead of producing two parts, the joystick will now be printed in one piece. This is made possible by 3D printing using the HSS process (high-speed sintering > more). A polymer plastic is used here, which is dyed black after printing.
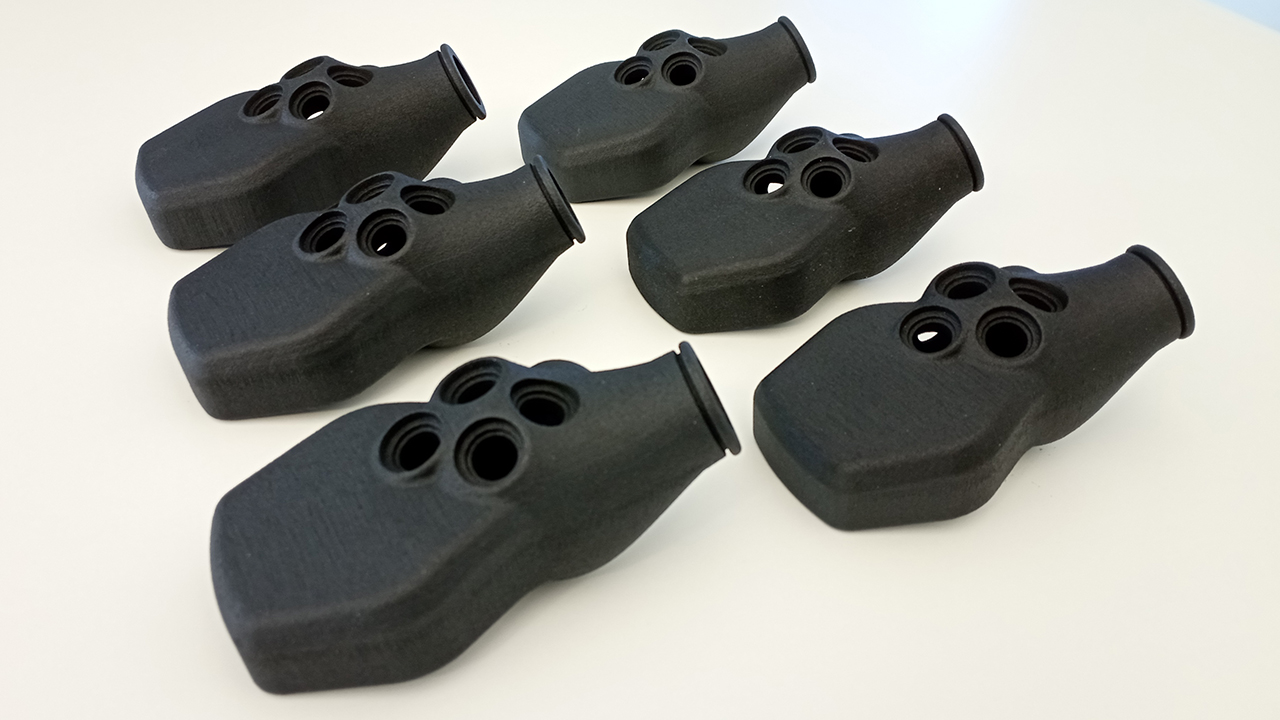
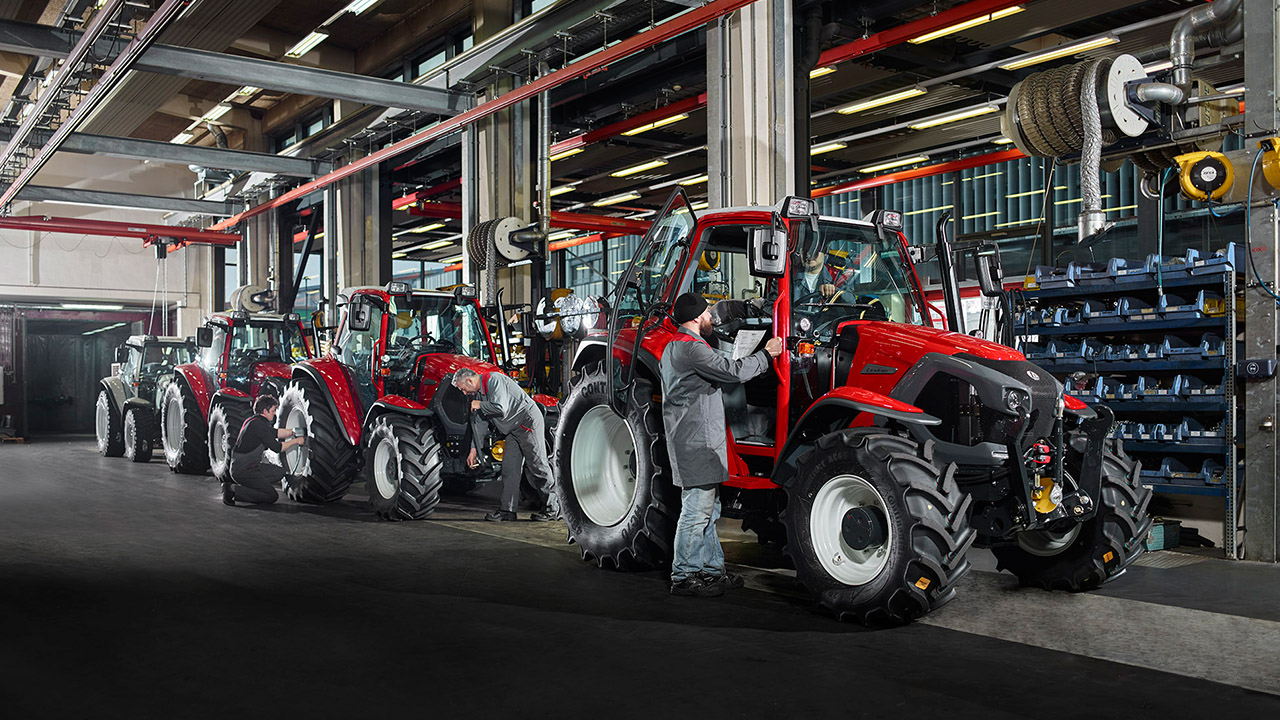
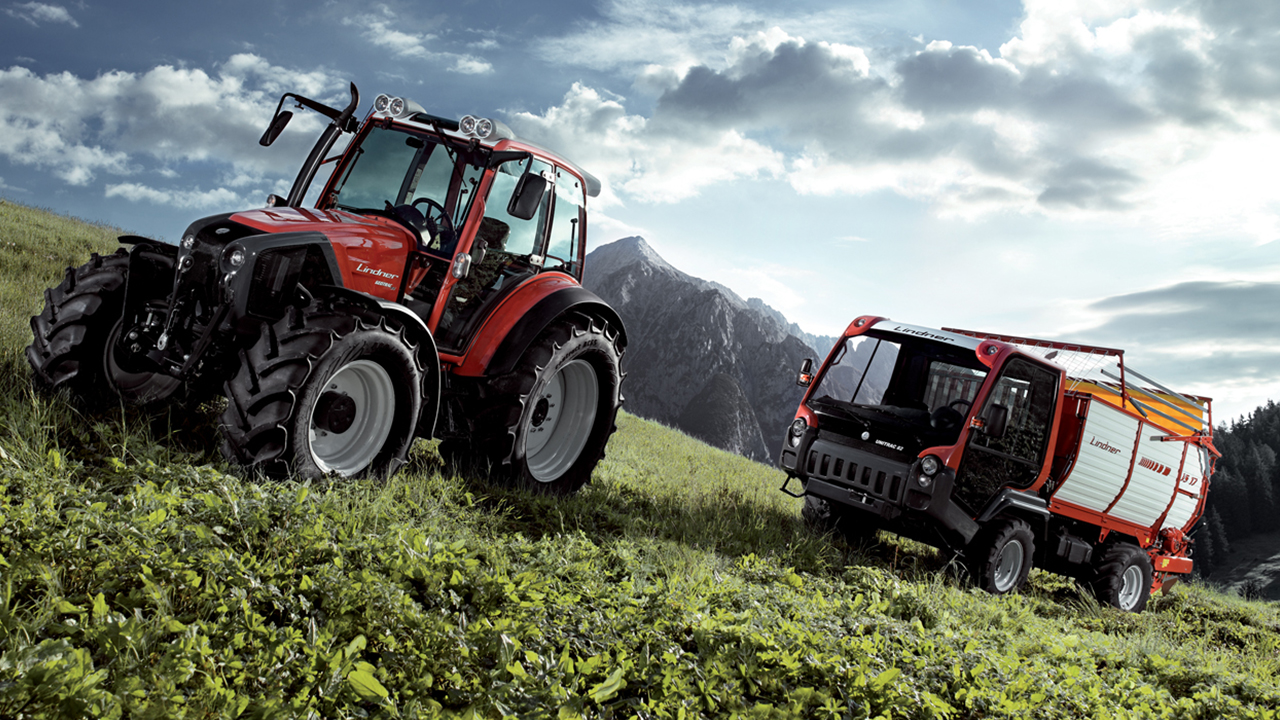
Advantages of 3D printing
Complex and small quantities
Due to the complex geometry and the relatively small number of units (approx. 300 units per year), 3D printing is currently the best solution for cost-effective series production. The flexibility of 3D printing also enables continuous further development of the control lever, as the geometry is not tied to expensive injection molding tools.
What you can do with 3D printing
Whether it’s a joystick for tractors, a buoy for helicopters (reference: Wucher), a complex functional component (e.g. Venturi nozzle) or an inexpensive spare part (e.g. cable holder) – 3D printing makes things possible that you may not even have thought of. Do you have a component where you have reached your limits? We will be happy to advise you and show you the best way to solve your challenge, free of charge and without obligation.
Diverse areas of application in 3D printing
From small series to large-scale production
However, 3D printing is not only used for repairs and maintenance. Entire product series can now also be manufactured quickly and cost-effectively using additive processes. Even complex designs are easy to implement – from small series to large-scale production.
Concept models and functional prototypes
Speed plays a decisive role not only in repairs and maintenance. Models or prototypes should also be produced as quickly as possible in order to react flexibly to the market.
With the help of 3D printing, you can quickly obtain a concept model of your product or already functional prototypes that can be put through their paces.
Component optimization
3D printing is also used to optimize components. To avoid production downtime due to repairs, components can be improved using a combination of simulation and 3D printing.
Thanks to the design optimization, the components are more resilient and the service life is increased. The weight of many components can also be optimized.