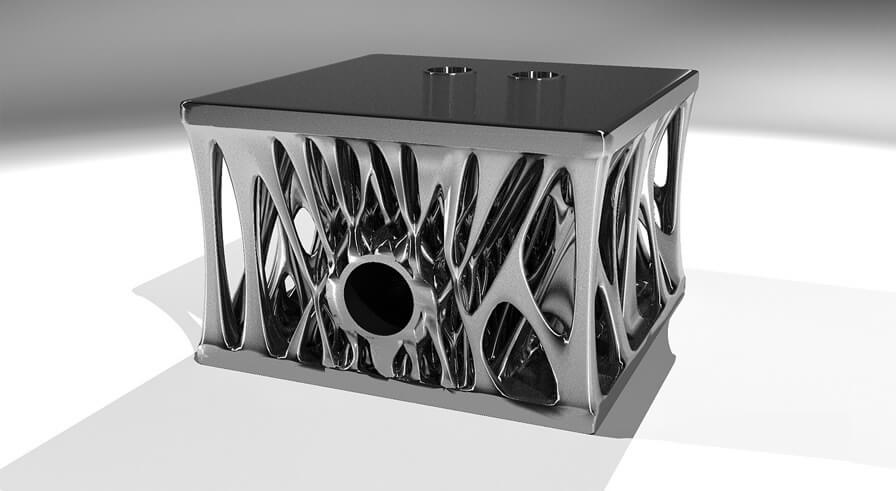
- Optimizations for sustainable material & energy savings
- Analysis combination of simulation and 3D printing
- Generative design as an optimization option
- Numerous examples of success in practice
- Profound expertise in topology optimization
Component optimization
Clever components can simply do more: sustainable material and energy savings with full stability and functionality
Would you like to optimize your component easily and avoid high additional costs as far as possible? WESTCAM makes it possible: with the clever combination of simulation and 3D printing.
Our component optimization service helps you to significantly shorten the entire optimization process. Time-consuming and cost-intensive material tests are replaced by simulation. The prototype is created quickly and cost-effectively using innovative 3D printing technology.
How we tackle it concretely
The process begins with you, the customer, specifying certain design objectives, ranging from functional requirements and material types to manufacturing methods and cost constraints.
Based on these requirements, a proposal is created three-dimensionally in the previously defined design space. This model is then produced using 3D printing and further verified.
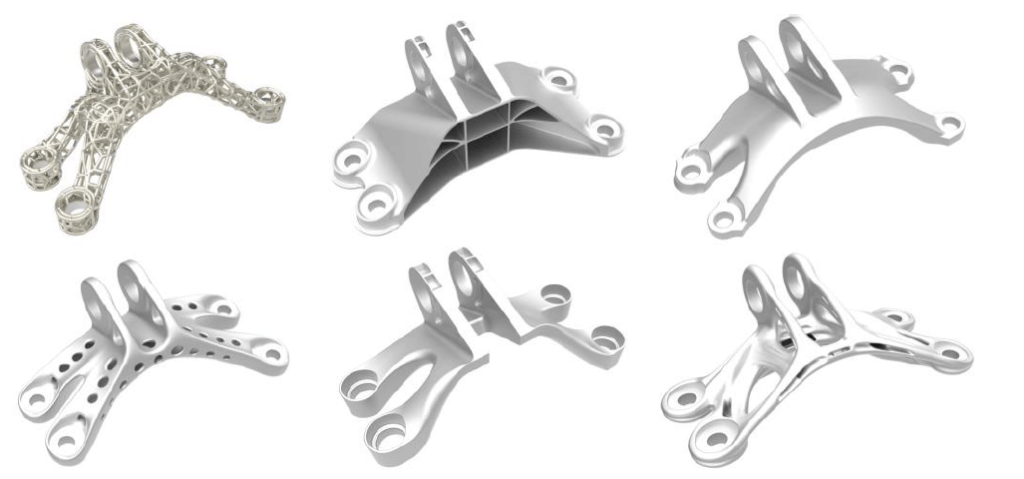
YOUR OPTIMIZED COMPONENT – ENGINEERED BY WESTCAM
These basic methods are used:
CAO(shape optimization)
CAO (Computer Aided Optimization) simulates the load-adaptive growth of biological force carriers.
This simulation is based on the determined mechanical stresses that result from the load and bearing conditions for any given design. In accordance with the axiom of constant stress, it causes a uniform stress distribution on the component surface through growth in highly stressed areas and optional shrinkage in understressed areas. This makes the component more resilient and increases its service life.
SKO (weight optimization)
SKO (Soft Kill Option) simulates the adaptive stress processes in the component.
Like the CAO method, the SKO method is based on the simulation of the growth rule of biological force carriers and is therefore a method from the field of bionics. The biological model is bone growth.
Highly stressed areas are stiffened and less stressed areas are softened and finally the unnecessary material is removed.
Frequently asked questions (FAQs)
Wozu dient die Bauteiloptimierung?
The less material a component has, the cheaper and lighter it is. It is therefore common practice to optimize components and hollow them out, for example. This saves material and production time. Where necessary, an additional layer of material can be applied or the component wall can be reinforced.
Thanks to modern 3D technology, optimization and redesign can already take place on the 3D model before the component is 3D printed and/or mass produced.
Another advantage of component optimization is that the simulation and calculation of the forces acting on the component in the software means that time-consuming material tests can be avoided. This means that the component can go into production more quickly.
Welche Vorteile hat die Bauteiloptimerung mittels 3D-Technologie gegenüber der klassischen Fertigung?
Component optimization in conventional production involves a great deal of effort and costs, as the production system has to be adapted and expensive tools are required.
In contrast, component optimization using 3D printing is significantly easier and more cost-effective, as only the CAD model needs to be changed. Likewise, fewer individual parts are usually required than with conventional production, which in turn reduces costs as well as planning and assembly costs.
In welchen Branchen wird Bauteiloptimierung angewendet?
Our 3D printing services are used by customers from various industries, for example in vehicle and automotive construction, aerospace technology, mechanical engineering, plant construction, the sports and leisure sector and medical technology.