CT industrial computed tomography
Deep insights into technical components
Modern CT systems use X-rays to create precise 2D images, which are processed into 3D volume data in a downstream reconstruction process. Based on this data, it is possible to identify defects, faults, internal features and assembly situations.
After generating a surface model, the geometric evaluation of the test specimen is also possible for dimensional inspection applications. This technology is particularly useful for quality assurance, fault diagnosis and the optimization of manufacturing processes.
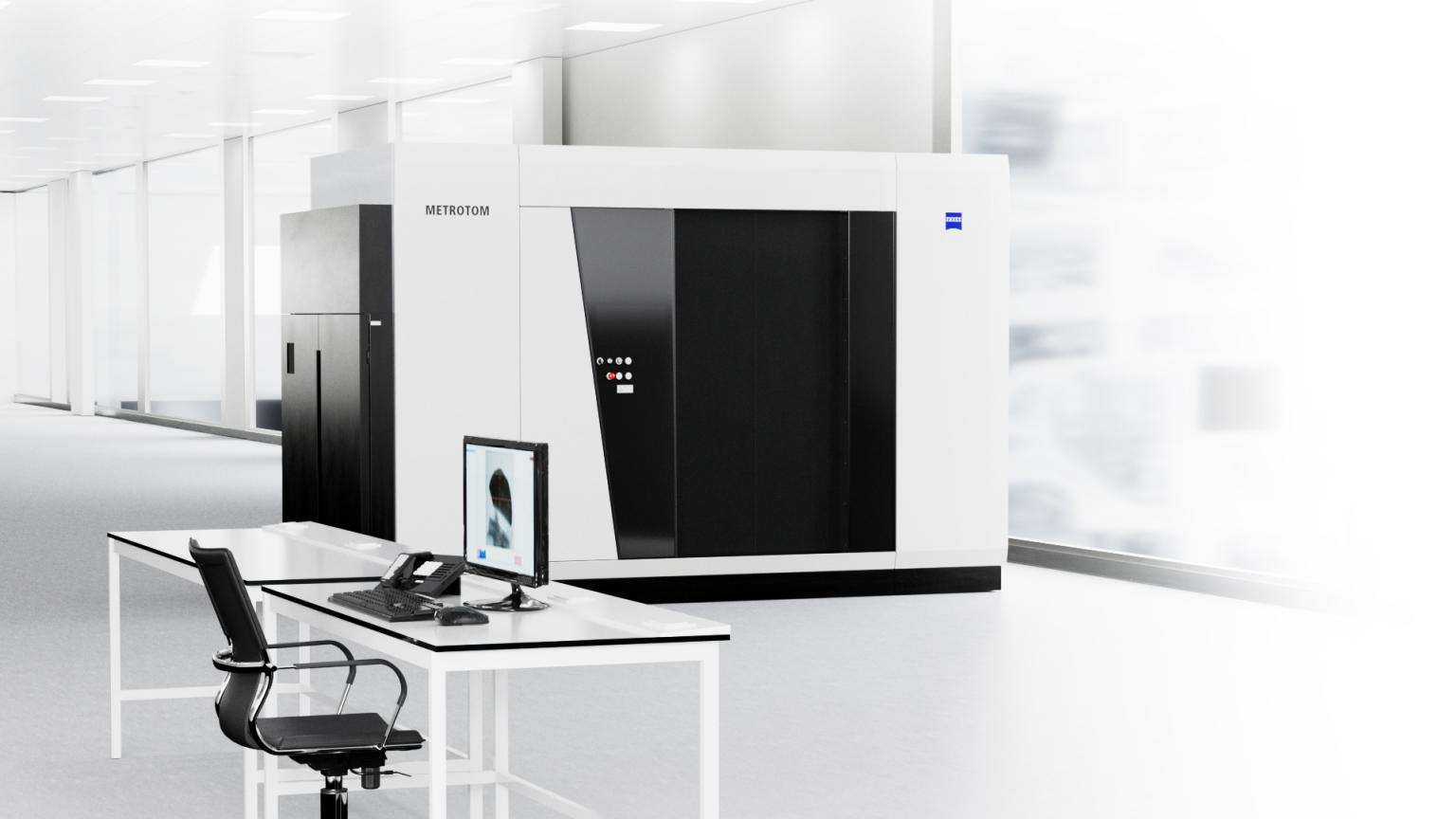
- Geometry analysis
- Volume analysis
- Defect detection
- Blowholes & inclusions
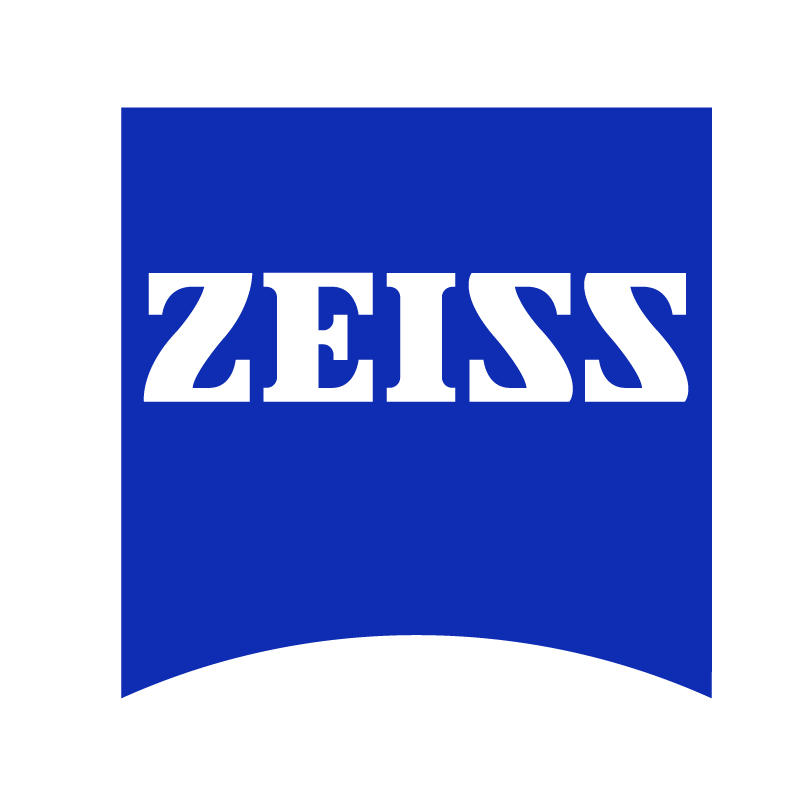
Data acquisition with ZEISS METROTOM
With a computer tomograph from ZEISS, you can perform even complex measuring and inspection tasks efficiently with just one X-ray scan.
The standard-compliant acceptance, the precision mechanics used and the sophisticated calibration procedure guarantee the traceability of the system. Linear guides and rotary table meet the highest standards of accuracy.
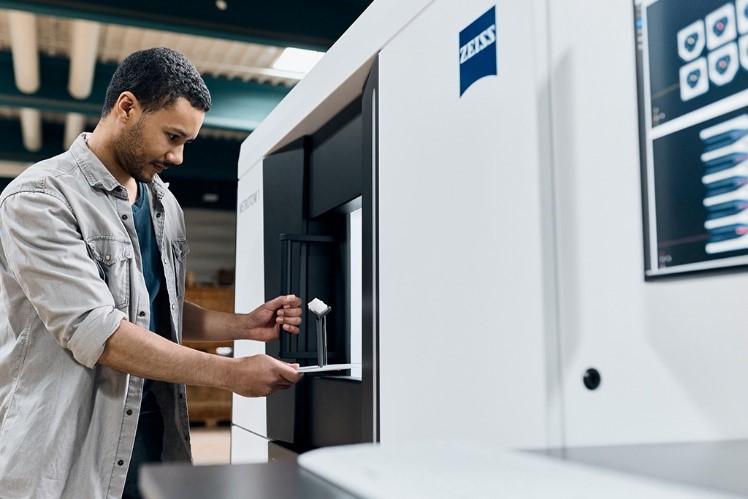
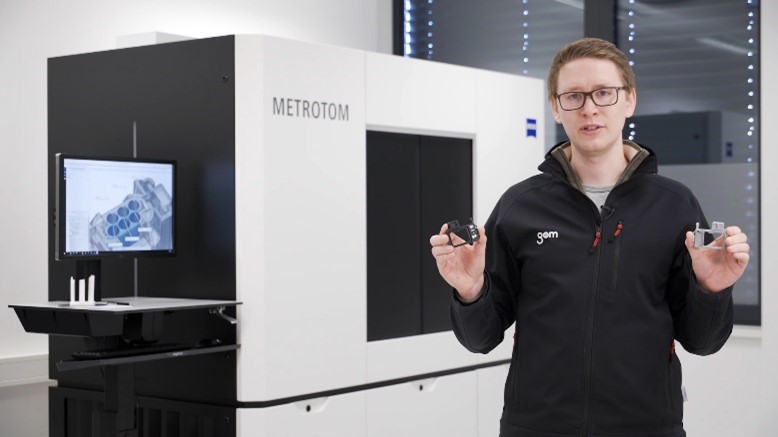
Advantages of X-Ray technology
Compared to full-surface 3D scanners, CT technology offers the advantage that a high-quality digital twin can be created regardless of the complexity and surface quality of the test specimen.
In addition to the dimensional accuracy assessment of the external geometry, countless analyses of internal component areas can be carried out.
Comprehensive CT data analysis in 3D
ZEISS INSPECT X-Ray is the name of the software for CT data acquisition and analysis of solid models. It can be used to create geometry evaluations as well as to analyze internal defects, cavities and assembly situations.
Efficient reporting functionality, automatisms and trend analyses are also part of the comprehensive tool.
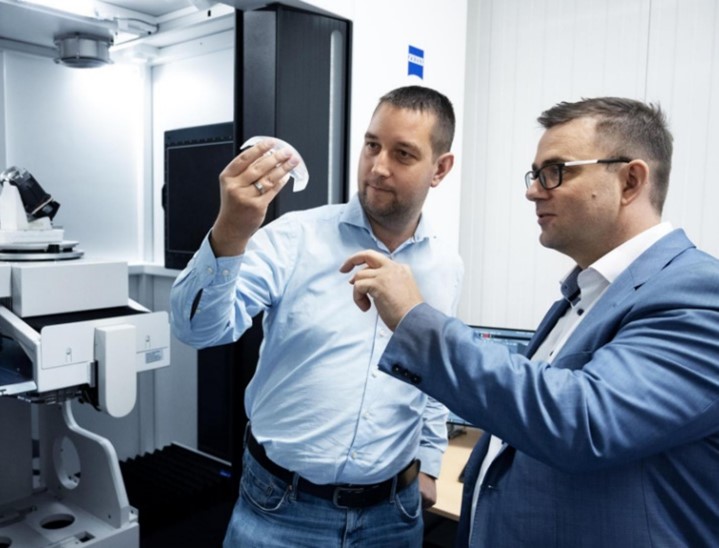
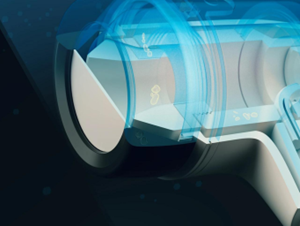
Inspection of volume models from other manufacturers
ZEISS INSPECT X-Ray also enables the import of third-party data and thus also offers users of alternative CT hardware access to efficient and automatable inspection processes.
Frequently asked questions (FAQs)
Was ist industrielle Computertomographie?
This refers to the three-dimensional measurement of technical components based on X-ray technology. The principle is similar to medical computed tomography, although in industrial CTs the radiation source and the detector are usually stationary and the component to be measured moves while the image is being captured.
This type of 3D-Metrology is primarily used for complex components that need to be analyzed in their entirety or also on the inside. The primary measurement result is a volume model in voxel format, which in most cases is converted into a full-surface STL format for further analysis purposes.
Welche Analysen können mittels industriellem CT durchgeführt werden?
The applications are very diverse. Among other things, the measurement data is used to evaluate the geometric dimensional accuracy of individual parts and components over their entire surface – especially if it is not possible to capture the entire surface using an industrial 3D scanner (depending on complexity).
The analysis of gas inclusions and blowholes is often used in the product development of plastic or cast components. The size, volume, number and distribution of inclusions can be evaluated easily and intuitively.
The evaluation of assemblies, e.g. fault analysis in the event of leakage problems, deformation of individual parts in the assembled state and the analysis of the general shoring situation are another major field of application.
Wie exakt sind industrielle CT-Vermessungen?
A fundamental distinction must be made between resolution and measurement accuracy:
The detector resolution provides information about the achievable measuring point distance of the CT at minimum magnification and is an indicator of the size at which surface structures can still be imaged. Typically, the resolution should be a factor of 5-10 smaller than the smallest feature to be detected on the component. (e.g. evaluation of a radius on the component with arc length = 1mm à spatial resolution of the scan = 0.1 to 0.2mm)
With many technical computer tomographs, the resolution can be positively influenced by changing the distance to the detector and by adjusting the component rotation. (magnification effect)
The measuring accuracy describes how precisely the generated measuring points lie on the actual component surface. Depending on the CT system used and the magnification, industrial CT systems from ZEISS achieve accuracies of up to 0.005 mm.
We advise you personally!
Gladly there for you
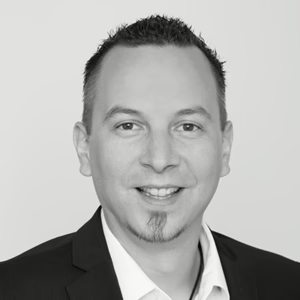